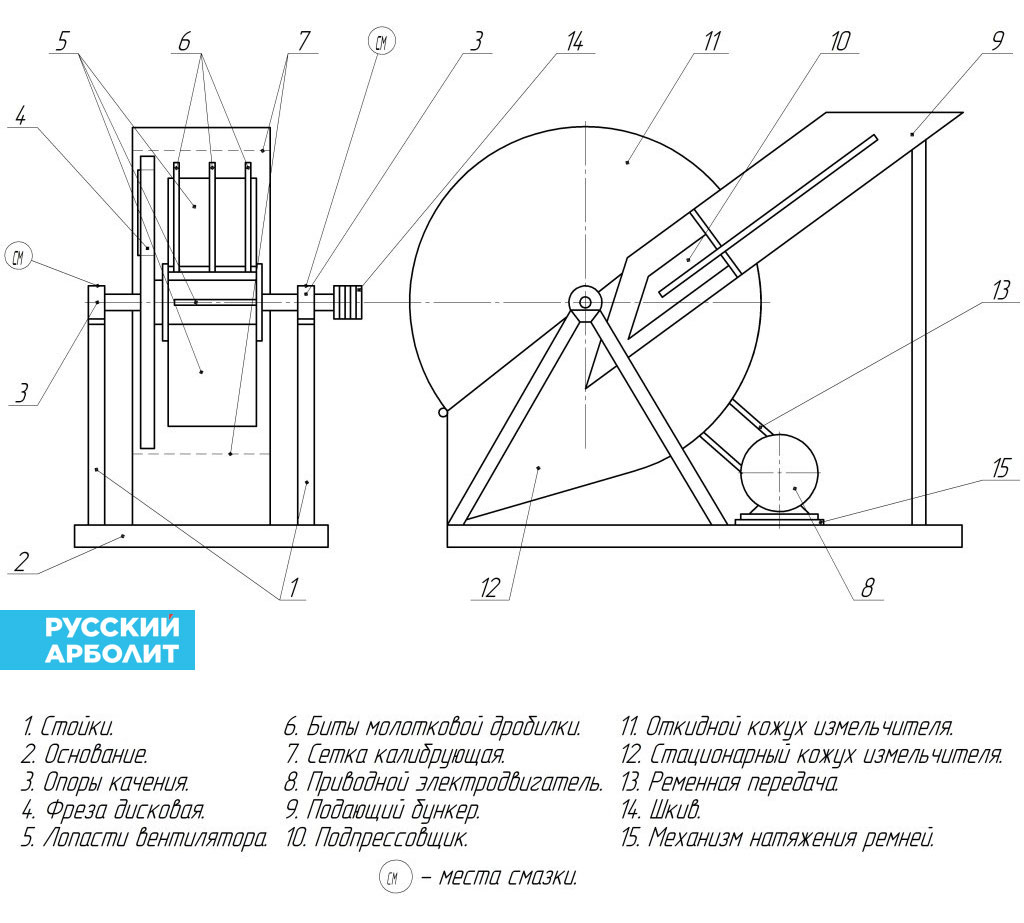
Как сделать щепорез для арболита своими руками: чертежи и схемы
Щепорез для арболита: принцип работы
Основными узлами станка являются рубильный диск с ножами и ротор с молотками и лопастями. Диск монтируется на рабочем валу, который приводится в движение с помощью шкива, соединенного посредством ремня с двигателем. Вал вращается в двух роликовых подшипниках, а двигатель установлен на раме.
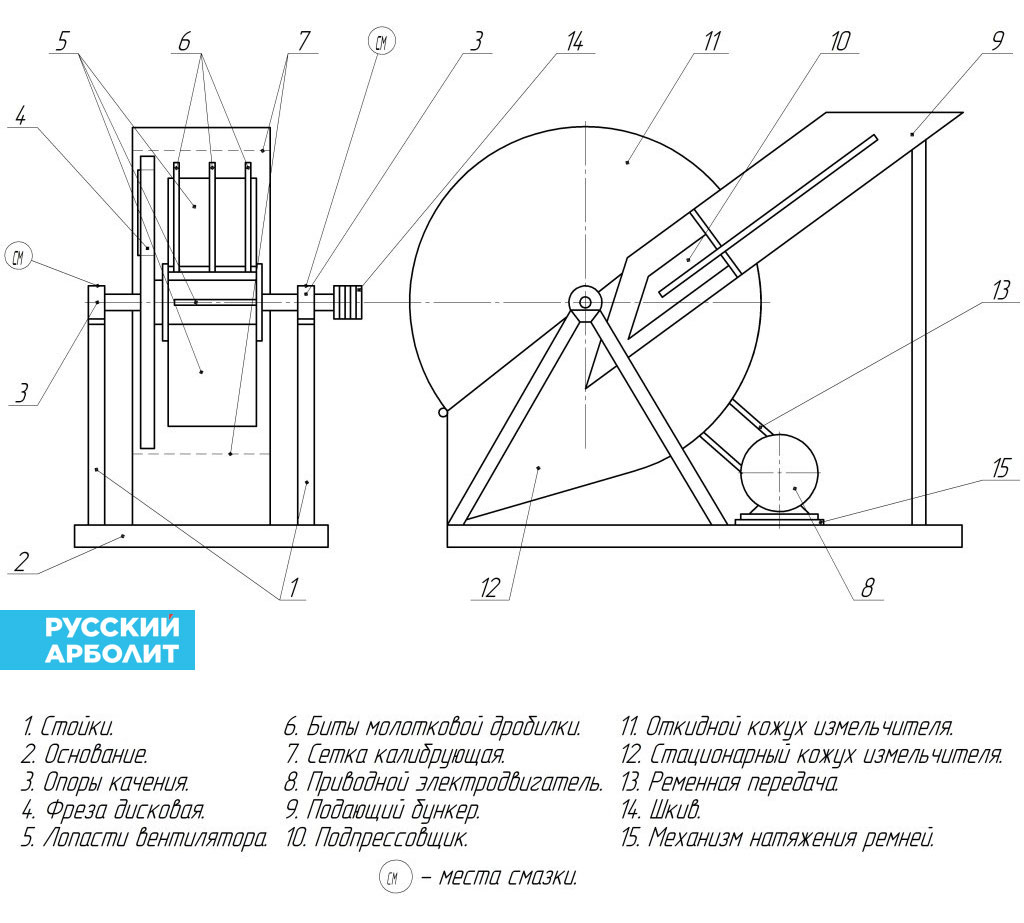
Подача сырья осуществляется вручную, то есть все, что подлежит переработке, закидывается по одному в приемный бункер, а затем древесные отходы уже сами затягиваются под работающие ножи и молотки. На завершающем этапе щепа с помощью лопастей попадает на сито и вылетает из щепореза через отверстие для выгрузки.
На входе приемный бункер выполнен в виде воронки для того, чтобы упростить подачу сырья для переработки и сделать этот процесс безопасным для рук.
Станок для изготовления щепы для арболита имеет следующие характеристики:
- мощность двигателя – 7,5 кВт;
- частота вращения на рабочем валу двигателя – 3000 об/мин;
- частота вращения вала, на котором закреплен диск с режущими ножами – 1500 об/мин.
При увеличении частоты вращения вала с диском какое-то количество древесного сырья может перемолоться в труху (естественно, это плохо), хотя производительность щепореза при этом возрастает.
Подготовка других элементов
Прежде чем конструировать щепорез своими руками, необходимо подготовить все детали. Для изготовления диска понадобится металлический лист толщиной 16-20 мм. Диаметр готового изделия должен быть примерно 300-350 мм. В центре делается отверстие, куда помещается шпонка, а по внешнему периметру — симметричные прорези. Через них будет отводиться стружка. Для крепежа ножей подготавливаются отверстия. Щепорез своими руками можно собрать с применением готового диска. В любом случае диск одновременно будет являться маховиком.
Для подготовки ножей, каждый из которых должен иметь два отверстия, чаще всего рекомендуют брать рессоры от легкового автомобиля. Отверстия углубляют, чтобы головки винтов «утапливались» в нож. Ножи для щепореза закрепляются с помощью болтов, которые откручиваются (закручиваются) шестигранным ключом. Этот факт объясняется тем, что болты под отвертку закручиваются не так плотно. Болт же под шестигранник легче удержать при закручивании гайки от проворота, он лучше прижимается к диску, пазы на головке не «слизываются».
Под молотками понимают плоские пластины металла, толщина которых составляет порядка 5 мм. Располагаются они на роторе. Это те детали, которые лучше купить уже готовые.
Читайте также: Пилочка и ацетон: безопасный способ снятия гель-лака в домашних условиях
Необходимо подготовить сито. Для этого берут любую металлическую емкость, от которой отрезается кольцо. В нем делают отверстия. Можно воспользоваться сверлом или пробойником конусного типа.
Далее организуется выталкивание стружки из машины. Для этого на второй стороне диска (противоположной ножам) привариваются поперечные планки. Они будут вращаться вместе с диском, тем самым подталкивая стружку наружу.
Основные узлы щепореза
Необходимые чертежи, по которым для производства арболита может быть изготовлена самодельная роторно-молотковая дробилка, представлены ниже. Так как оборудование самодельное, то и размеры деталей придется подбирать, исходя из собственного материала.
Дробилка для арболита, изготовленная своими руками по желанию может иметь питание в 220–380 В и состоит из следующих узлов:
- Металлический корпус со съемным (или откидным) кожухом (11,12).
- Свободно вращающиеся биты с молотками для производства непосредственно щепы, секторально разделенные отбойниками (6).
- Диск с закрепленными на нем ножами (4).
- Калибрующее сито с отверстиями Ø 15–20 мм (7).
- Бункер для подачи отходов из древесины (9).
Рабочие чертежи разных щепорезов могут отличаться размерами и наличием тех или иных узлов, но принцип работы остается одинаковым. После подачи на оборудование напряжения 220 В электродвигатель предает свое вращение при помощи клиноременной передачи на барабан с лезвиями (4) через шкив (14) и вал. Нужно только закладывать в подающий бункер древесные отходы, которые сразу перерабатываются в щепу оптимальной длины (до 25 мм).
Собрав щепорез для арболита своими руками и выдержав расстояние между молотками в дробилке арболита можно производить щепу длиной до 25 миллиметров и шириной около 5 миллиметров. Такая щепа идеально подходит для изготовления арболитовых блоков или приготовления монолитного арболита.
Как самостоятельно сделать дисковый щепорез
Чтобы сделать своими руками щепорез, нужно найти готовый или сделать собственный чертёж с расчётами. Нет необходимости готовить целую проектную документацию. Достаточно будет начертить или даже нарисовать от руки схему всех частей механизма с размерами.
Нам понадобится:
- Мотор;
- Дисковые пилы с победитовыми напайками в количестве 20 – 25 штук;
- Вал с тем же диаметром, что и посадочное место пил;
- Гайки и шайбы того же размера;
- Подшипники;
- Шкивы и плотный ремень;
- Профтруба, уголок или швеллер из толстого металла;
- Листовое железо толщиной 4-12 мм для маховика, защитного кожуха и загрузочного бункера;
- Плотные пластиковые шайбы по количеству дисков.
Этап 1. Собираем режущий блок
Дисковые пилы по дереву можно купить в магазине. Обойдётся это не дорого. Набираем их на вал, прокладывая их шайбами. Делать это нужно потому, что толщина победитовой напайки больше толщины самого диска.
Чтобы пилы не мешали друг другу, и между ними был необходимый зазор, нужно отделить их друг от друга. Есть вариант приваривать каждый диск к валу.
Но многие умельцы собирают эту конструкцию, затягивая с двух сторон гайками. На гладком валу для этого придется нарезать резьбу в месте посадки дисков.
Можно использовать в качестве вала резьбовую шпильку, в этом случае все проще: на шпильку М20 набираются дисковые пилы с посадкой 20мм и затягиваются с обеих сторон гайками М20.
Такая конструкция имеет преимущество – в случае выхода из строя одного или нескольких дисков их проще заменить новыми. Диски лучше расположить так, чтобы зубья их находились со смещением друг относительно друга или в хаотичном порядке.
Это предотвратит чрезмерную нагрузку на пилы и на двигатель. Расстояние между пилами будет определять величину производимой щепы. Но слишком большое расстояние чревато тем, что мелкие ветки будут застревать между пилами или накручиваться на вал.
Для вращения вала понадобятся два подшипника. Подойдут, например, подшипники от старых ВАЗ 2103, ВАЗ 2105, ВАЗ 2107, стоящие на промежуточном вале коробки передач (размер 20*50*20,6) или на опоре вала рулевого управления тех же авто (размер 20*37,5*22).
Хорошие подшипники стоят в колесах строительных тележек, выдерживающих до 300 кг.
Этап 2. Делаем раму
Из профильной трубы или уголка свариваем раму, на которой будет установлен наш режущий блок. Еще одну готовим для двигателя.
Платформу для него делаем с возможностью регулировки натяжения ремня. Для этого просверливаем в раме два удлиненных отверстия М12 – М14.
Этап 3. Готовим рабочий бункер
Из листа металла толщиной не менее 8 мм нарезаем полосы, которые затем свариваем в конструкцию, представленную ниже. Это бункер, в котором и будет происходить процесс измельчения древесины ножами.
Прочность бункера важна, поскольку он будет выдерживать удары летящих веток. Можно усилить его уголками, которые будут играть роль рёбер жёсткости.
Напротив дисковой конструкции устанавливаем неподвижный нож (контрнож). Именно в него будут упираться разрезаемые ветки.
Этап 4. Делаем маховик
Из железа толщиной 10-12 мм вырезаем круг примерно 300 – 350 мм диаметром. Он должен быть тяжелым, так как будет выполнять роль маховика.
Поскольку при мгновенной остановке двигателя в момент выключения может произойти заклинивание крупных кусков дерева, в момент последующего пуска произойдёт резкий нагрев и даже выход из строя.
Маховик, делая остановку постепенной, поможет избежать подобных стопоров. Делаем посадочное отверстие по диаметру вала и сажаем наш маховик.
Этап 5. Устанавливаем двигатель и режущий блок
На рабочий вал устанавливаем шкив. Подойдет снятый с моделей отечественного автопрома. Лучше найти двух- или трехпоточный. Тогда впоследствии можно будет перебрасывать ремень и регулировать обороты нашего щепореза.
Двигатель ставим так, чтобы его ось была параллельна оси дисков, избегаем перекосов.
Наш щепорез готов.
При желании можно оборудовать его колесной парой для удобства транспортировки.
По такому принципу можно собрать и роторно-молотковый щепорез. Отличаться он будет только режущим блоком.
Сборка устройства
Создавая самодельный щепорез, в центре режущих элементов нужно проделать отверстие под вал, а также три паза и ряд дополнительных отверстий. Они предназначаются для перемещения перемолотых частиц древесины в сектор с молотковыми битами. Если в домашних условиях сложно найти готовые ножи, их можно создать из автомобильной рессоры.
Для этого ее нужно разрезать на небольшие участки, а затем просверлить в них пару отверстий, обработать и отшлифовать. Также заготовку тщательно натачивают и еще раз пропускают через шлифовальную машину. В качестве молотков для дробления щепы задействуют небольшие металлические полоски. Оптимальная толщина должна составлять не меньше 1 сантиметра.
Сито изготовляют из листа металла длиной 10 сантиметров. Из заготовки сваривают ровный цилиндр диаметром 30 сантиметров, а затем в нем делают подходящие отверстия. Диаметр этих отверстий составляет 0,7-1,5 мм.
Кожух и воронки создаются из листового железа толщиной от 1 см. Подходящий материал нужно разрезать и сварить в форме короба. Чтобы усилить конструкцию, в разных ее сторонах нужно разместить дополнительные ребра жесткости. Размеры корпуса должны быть достаточно большими, так как в них будет находиться режущий узел. При этом между стенками короба и ножами должен присутствовать минимальный зазор в 2-5 см.
При установке дробильных механизмов на часть вала, который установлен на подшипниках, монтируют молоточки и режущие доски. Затем вырезают два раструба: первый предназначается для подачи исходного сырья, а второй — для выхода готовой щепы.
Резервуар под древесные отходы лучше изготовлять из прочного металла, размещая его под небольшим углом касательно кожуха. Двигатель фиксируют на основной раме, и только после этого к нему проводят шкивы. Рабочие узлы и механизмы машины соединяют посредством ремней или цепей. Кстати, для такой задачи отлично подходят автомобильные ремни. Для сваривания рамы задействуют металлические уголки или трубу. Ее размеры выбираются индивидуально.
Где брать детали и материалы?
Поскольку одной из причин, побуждающих к самостоятельному изготовлению шредера, является желание сэкономить, то очень важно сократить траты на детали и материалы.
Помочь в этом могут пункты приема черного и цветного лома, а также различные предприятия, на балансе которых есть старая техника. Также могут помочь деревообрабатывающие предприятия и цеха, особенно те, где недавно было модернизировано оборудование.
Для изготовления каркаса роторно-молотковой машины можно использовать стальной уголок или швеллер, причем не обязательно новый, главное, чтобы металл не был поврежден ржавчиной.
Корпус станка, он же защитный кожух вокруг роторно-молоткового механизма, а также защитный кожух вокруг ременной или цепной передачи, можно сделать из листового металла толщиной 0,8–2,5 мм.
Этот же металл подойдет для изготовления приемного кожуха. Такой металл можно срезать с кузова некоторых автомобилей, а также из различных ограждений и настилов.
Электромотор можно снять со старого станка или различного электрического оборудования. Возможно, ему потребуется заменить подшипники, но это обойдется дешевле покупки нового электромотора нужной мощности.
Там же можно подобрать и шкивы необходимого размера, а также электрооборудование, необходимое для запуска и работы мотора.
Для изготовления ротора можно использовать как листовую сталь, так и подходящий по диаметру маховик от автомобильного двигателя. Однако в этом случае необходимо будет вставить в него и приварить вал молоткового измельчителя.
Для изготовления ножей хорошо подойдет рессора от легкового автомобиля. Опытный кузнец сможет придать ей нужную форму и правильно закалить, благодаря чему нож будет не только острым, но и прочным.
Если у вас есть ненужный или временно простаивающий мотоблок, то с него можно снять мотор. Это позволит сделать щепорез более мобильным, особенно если поставить его на прицеп для легкового автомобиля.
Если на моторе предусмотрен вал отбора мощности (ВОМ), то можно подключать щепорез к нему без разборки мотоблока.
Использовать мотор от бензопилы нежелательно из-за недостаточной мощности, исключение составляют лишь бензомоторы с объемом 60 см3 и больше.
Минус мотора из бензопилы в том, что его можно подключить к валу измельчителя лишь через цепную передачу, поэтому довольно сложно найти подходящую цепь и звездочку на вал.
Электромоторы из болгарки, электрорубанка, циркулярки и другого ручного инструмента не подходят для создания нормального измельчителя, зато из них на основе тех же чертежей можно сделать своими руками веткоруб небольшого размера, то есть щепорез, предназначенный для измельчения тонких веток.
От нормального щепореза он отличается размерами и принципом работы. В таком самодельном веткорубе древесину измельчает шестерня с ножами, которая рубит ветки на кусочки длиной 0,5–3 см, то есть нормальную щепу с его помощью не получить, но для утилизации веток он подходит.
Какой тип самодельного измельчителя выбрать, и как его сделать?
В интернете можно встретить и взять бесплатно чертежи с размерами и описание различных самодельных щепорезов, но большая часть – это теоретические измышления.
Ничего плохого в этом нет, но лучшим критерием истины является практика, поэтому необходимо посмотреть на реальную работу таких изделий и почитать отзывы о работе этих устройств, изложенные на различных форумах.
Многие щепоколы эффективно используют для измельчения бумаги, резины и других материалов, ведь принцип действия полностью неизменен – устройство рубит или разрезает материал, превращая его в мелкие частицы.
Поэтому мы подготовили ссылки на темы, связанные с изготовлением и использованием самодельных измельчителей различных типов:
- Форумхаус;
- Форумы Лесной Отрасли;
- Мастеровой;
- Металлический форум.
Роторно-молотковый
Наиболее универсальным и простым в изготовлении является роторно-молотковый измельчитель.
Станок этого типа измельчает любые древесные отходы, появляющиеся как в результате станочной обработки деловой древесины, так и после обрезки сада.
Для эффективного измельчения древесины на заводских и самодельных устройствах должны быть соблюдены следующие условия:
- размер измельчаемого материала должен быть меньше размера приемного окна;
- на древесине не должно быть крупных комьев земли, цемента или металлических фрагментов;
- для получения чистой щепы необходимо использовать окоренную древесину.
Барабанный
Изготовление барабанного измельчителя затруднено тем, что довольно сложно найти барабан нужного размера.
Если взять фрезу от фуговального станка, то она будет производить лишь очень мелкую стружку.
Это связано с тем, что фреза из фуганка изначально рассчитана на очень большую скорость вращения, благодаря чему ее инерции хватает для срезания сучка или скрученных волокон.
Для увеличения размера отходов необходимо снижать скорость вращения в сотни раз, а значит, во столько же раз увеличивать крутящий момент, приложенный к фрезе. В результате инерция фрезы не будет участвовать в измельчении древесины, а значит, потребуется еще большее увеличение крутящего момента.
При вращении фрезы на такой скорости ножи будут не резать, а давить древесину, для чего потребуется огромная мощность.
Приложение такой силы невозможно передать с помощью ремней, а шестеренчатая передача будет испытывать колоссальные нагрузки.
Ведь помимо зубьев шестеренок нагрузки испытывают и места соединения валов с шестернями. Если их делать путем фрезерования (монолитными), то они получатся огромными, если же использовать шлицевую и, тем более, шпоночную фиксацию, то велика вероятность, что шестерни провернет на валу. Особенно, если придется измельчать толстую древесину.
Кроме того, фуговальный барабан (фреза) рассчитан на воздействие вдоль волокон, где гораздо меньше сопротивление движению ножа, а в щепорезе основным режимом будет воздействие поперек волокон с огромным сопротивлением древесины.
Поэтому для фуганка необходим диаметр фрезы в 3–5 раз меньше, чем для измельчительной машины. Также необходимо увеличить расстояние между ножами, что позволит делать более толстую щепу.
Еще один существенный недостатокфуговального барабана, вращающегося на высокой скорости, в том, что даже при вертикальной подаче, когда древесина опускается под собственным весом, толщина щепы не превышает долей мм.
При скорости вращения вала в 3000 об/мин ножи за секунду проходят через измельчаемые ветки и другие отходы 200 раз, то есть промежуток между воздействиями ножа составляет 0,005 с.
Какой путь успеет пройти ветка, если учитывать, что каждый удар ножа немного отталкивает ее вверх? Поэтому для барабанных щепорезов оптимальная скорость вращения вала составляет 100–300 об/мин, при этом на валу устанавливают 2–3 ножа.
То есть даже при максимальных оборотах и количестве ножей за секунду пройдет максимум 15 ударов, а при минимальных настройках 3–4 удара в минуту.
Дисковый
Этот измельчитель состоит из нескольких пильных дисков, насаженных на общий вал и разделенных шайбами. При этом ширина щепы равна расстоянию между дисками. В теории все просто, но в интернете нет ни одного видео с работой такого щепореза.
На некоторых форумах пользователи рассказывали о своем опыте работы с таким устройством, и все отзывы носят негативный характер.
По их словам, такой щепорез обладает очень маленькой производительностью, а междисковое пространство быстро забивается, из-за чего его приходится чистить несколько раз в день.
Шредер
Этот вид щепорезов предназначен для грубого измельчения древесины, которая содержит гвозди и другие небольшие металлические фрагменты. В промышленных одновальных устройствах его основу составляет литой барабан большого диаметра, на котором пайкой или болтами закреплены ножи.
В двухвальных шредерах вместо литого барабана делают шестигранный вал, на который надевают зубчатые насадки.
Причем ширина насадок и пространства между ними подобрана так, чтобы свободное пространство на одном валу превосходило ширину насадки другого вала на доли мм.
Благодаря такой точности изготовления оба вала работают по принципу ножниц и эффективно разрезают раздробленную щепу.
Сделать такие валы самостоятельно невозможно, а изготовление на заказ с такой точностью, да еще и из твердых стальных сплавов обойдется дороже покупного вала в сборе для щепореза.
Ведь при промышленном производстве ножи и отделяющие их проставки изготавливают штампованием, а при ручном изготовлении их придется в лучшем случае фрезеровать из листа.
Если же мастер не возьмется за такую работу, то сначала придется сделать матрицы для отливки, затем отлить из инструментальной стали и проковать, после чего фрезеровать, чтобы довести до нужной формы. Причем каждую деталь придется делать отдельно, из-за чего общая стоимость такого вала составит сотни тысяч рублей.
На некоторых форумах выкладывают видео работы самодельных шредеров из мощных шестеренок или оснащенных двумя согласованными валами, изготовленными из стальных уголков и самодельных ножей (заточенные рессоры).
Сколько вам будут стоить такие ножи из рессор от легкового автомобиля, будет зависеть от того, на каких условиях они вам достанутся.
Такие устройства рубят даже довольно толстые ветки, но на выходе получается не щепа, а обрубки, толщина которых равна толщине ветки, а длина составляет 5–10 см.
Использовать такую измельченную древесину можно лишь в качестве топливной щепы при условии, что подающий шнек котла рассчитан на работу с таким материалом.
Подготовка корпуса
Щепорез своими руками начинают изготавливать с подготовки необходимых деталей. Часть из них можно приобрести в местах сбора металлолома, а некоторые придется выточить у токаря.
Для изготовления корпуса понадобится лист металла с толщиной 3-5 мм. Из него с помощью трафарета вырезается нижняя и верхняя часть. Трафарет напоминает соединенные вместе круг и прямоугольник. Причем важно выбрать такие размеры, чтобы диаметр круга был больше диска с закрепленными ножами на 3-5 см. Боковой стенкой будет служить полоска металла. Понадобятся также два «бочонка»», которые можно вырезать из арматуры. В них делается резьба. Благодаря им соединяются верхняя крышка и корпус.
Соединяются части с помощью сварки. Сначала сваривается нижняя пластина с боковой полоской металла. После этого проверяется, вместится ли диск с ножами. Если все подходит, приступают к сварке «бочонков», которые соединяются с боковой и нижней сторонами. Все швы провариваются с двух сторон.
В корпусе необходимо подготовить отверстие для вала. В крыше делается отверстие для того, чтобы можно было вместить ветки. Оно выполняется под определенным углом, за счет чего ветки не выбрасываются назад.
Изготавливаем щепорез для арболита своими руками
Некоторые детали, чертежи которых представлены ниже, необходимо выточить на токарном станке, остальные можно изготовить своими руками в домашних условиях.
Основные размеры щепореза для арболита
Диск с ножами
Диаметр диска составляет около 300-350 миллиметров, а толщина – около 20 миллиметров. Чтобы предотвратить заклинивание больших и твердых кусков древесины, диск должен работать как маховик. Поэтому его надо сделать тяжелым. Для диска берем металлическую заготовку либо вырезаем его из листовой стали; затем пропиливаем в нем одно центральное отверстие для посадки на вал (учитывая шпоночное крепление), несколько монтажных отверстий и 3 паза, через которые отрезанные части древесины попадают под вращающиеся молотки.
Рубильный диск с ножами
Для изготовления ножей используем автомобильные рессоры. В каждом ноже делаем два отверстия с последующим их зенкованием (чтобы головки винтов были максимально утоплены) и крепим их к диску с помощью болтов с потайной головкой под шестигранник, которые обеспечивают плотное и надежное соединение, а также не позволяют болтам проворачиваться во время обжатия гаек с противоположной стороны.
Молотки
Вал и крепление для молоточков
Молоточки и приваренный отбойник
Молотки – это плоские пластины (толщиной около 5 миллиметров), которые расположены на роторе. Они осуществляют дополнительное измельчение щепы. Молоточки лучше купить готовые. Расстояние между молотками в дробилке арболита 24 мм.
Расстояние между молотками в дробилке арболита
Сито для щепореза
Для изготовления сита, внутри которого будет располагаться растирочная камера, нужен металлический цилиндр Ø 300–350 мм изготавливаемый из металлического листа длиной L 942–1100 мм. В этом цилиндре пробиваются ячейки диаметром 8–12 мм. Просверливать их нежелательно – края ячеек должны быть острыми или рваными, поэтому отверстия рекомендуется проделать пробойником или керном нужного диаметра.
Защитный кожух, воронка, приемный бункер и рама
Для защитного кожуха, и воронки для приемного бункера подойдет листовое железо толщиной 8–12 мм. Листы нарезаются в размер и свариваются в конструкцию так, как указывают чертежи. Нарезаем все детали по заранее подготовленным «выкройкам» (их делаем из плотного картона) Ребра жесткости делаются из уголков, швеллеров или труб.
Защитный кожух
Важно! Сам режущий узел не должен цепляться за стенки корпуса, поэтому чтобы режущий узел свободно размещался в корпусе, диаметр маховика должен быть меньше размера корпуса на 30–50 мм.
Оборудование дробильного узла: цапфы вала, на которые необходимо насадить опорные подшипники, плюс била (молотки) и режущий диск. Следующий шаг по изготовлению щепореза — нужно вырезать отверстия для рабочего вала, а также входные и выходные раструбы для подачи сырья и выхода щепы.
Рабочий вал
Приемный бункер приваривается к корпусу под углом. Механический и электрический приводы монтируются в последнюю очередь: на раму крепится электродвигатель, затем шкивы требуемого диаметра, и все узлы соединяются ременной передачей. Для этого можно использовать обычные автомобильные ремни подходящего диаметра.
Рама
Двигатель
От вида двигателя зависят производительность щепореза и объемы затрат на эксплуатацию. Экологичный электродвигатель не очень шумит, намного легче ДВС, но менее мощный, чем его «собрат». К тому же работа щепореза на электротяге зависит от скачков напряжения в электросети.
Агрегат на бензиновом, более мощном двигателе, работает дольше, больше и он не зависит от розетки электропитания. Но ДВС очень шумит, загрязняет воздух, требует ухода и его постоянно надо заправлять.
Если собранный щепорез для арболита соответствует требованиям точности и в соосности не будет разбега, то можно применить не ременное соединение, а соосную схему — можно подключить валы через муфту.
Подготовительный этап и изготовление
Прежде чем приступить к изготовлению щепореза, необходимо найти чертежи станка (например, в Интернете введя в Яндексе поисковый запрос «чертежи щепореза» ) с проставленными размерами, ведь чертежи в любом случае понадобятся: и при условии, что вы сами по ним будете изготавливать необходимые детали, и в случае, если вам придется обращаться к специалистам. Нет нужды выдумывать что-то оригинальное (все оригинальное уже придумано до нас), просто попытайтесь собрать свой щепорез (подобно заводскому), используя те детали и материалы, которые сможете раздобыть. Иногда необходимые узлы можно найти в пунктах по приему металла (и вал, и внешний шкив, и втулку и так далее). А что не найдете – изготовите собственноручно или попросите токаря (слесаря).
На начальном этапе очень важно определиться с общим количеством необходимого металла, габаритами опорной площадки агрегата (независимо от размеров готового щепореза), а также с видом двигателя.
Какой двигатель выбрать
От вида двигателя зависят производительность щепореза и объемы затрат на эксплуатацию. Экологичный электродвигатель не очень шумит, намного легче ДВС, но менее мощный, чем его «собрат». К тому же работа щепореза на электротяге зависит от скачков напряжения в электросети.
Агрегат на бензиновом, более мощном двигателе, работает дольше, больше и он не зависит от розетки электропитания. Но ДВС очень шумит, загрязняет воздух, требует ухода и его постоянно надо заправлять.
Диск с ножами
Диаметр диска составляет около 300-350 миллиметров, а толщина – около 20 миллиметров. Чтобы предотвратить заклинивание больших и твердых кусков древесины, диск должен работать как маховик. Поэтому его надо сделать тяжелым. Для диска берем металлическую заготовку либо вырезаем его из листовой стали; затем пропиливаем в нем одно центральное отверстие для посадки на вал (учитывая шпоночное крепление), несколько монтажных отверстий и 3 паза, через которые отрезанные части древесины попадают под вращающиеся молотки.
Для изготовления ножей используем автомобильные рессоры. В каждом ноже делаем два отверстия с последующим их зенкованием (чтобы головки винтов были максимально утоплены) и крепим их к диску с помощью болтов с потайной головкой под шестигранник, которые обеспечивают плотное и надежное соединение, а также не позволяют болтам проворачиваться во время обжатия гаек с противоположной стороны.
Молотки
Молотки – это плоские пластины (толщиной около 5 миллиметров), которые расположены на роторе. Они осуществляют дополнительное измельчение щепы. Молоточки лучше купить готовые.
Сито для щепореза
Для изготовления сита понадобится цилиндрическая емкость из металла, в которой с помощью сверла или конусного пробойника делаем отверстия. Работа кропотливая – придется слегка помучиться, но результат стоит того.
Корпус, воронка для приемного бункера и рама
Для корпуса, выполняющего защитную функцию, и воронки для приемного бункера подойдет листовое железо, из которого нарезаем все детали по заранее подготовленным «выкройкам» (их делаем из плотного картона) и свариваем.
Важно! Сам режущий узел не должен цепляться за стенки корпуса, поэтому разница в их диаметрах должна составлять 30-50 миллиметров.
Раму свариваем из уголка и швеллера, а укрепляем трубами.
Правила сборки станка
Необходимо строго выдерживать последовательность сборочных операций.
- Собирается измельчительный узел. На вал «насаживаются» диск с ножами, молоточки и подшипники внутри своих корпусов.
- На станину устанавливается нижняя стационарная часть корпуса.
- Внутрь вставляется измельчительный узел с ситом вместе, первый должен быть вставлен во второй.
- Измельчитель упирается на станину посредству подшипников, которые к раме тут же крепятся болтами.
- Сито надо прикрепить к неподвижной части корпуса винтами или болтами. Для этого к нему заранее привариваются ушки.
- На торчащий из одного подшипника конец вала насаживается большой шкив.
- Устанавливается электродвигатель, надевается на шкивы ремни.
- Приваривается или присоединяется болтами воронка к корпусу щепореза.
- Устанавливается на петли верхняя откидная часть корпуса.
Можно считать, что измельчитель древесины для арболита своими руками сделан. Остается лишь провести электромонтаж и первый пуск оборудования. Для электромотора требуется подводка трех фаз и установка подобранного под его мощность автомат. Вариантов электромонтажа два:
- собрать отдельный блок и установить с кнопкой пуска прямо на станине;
- кнопку оставить на станке, а автомат смонтировать в распределительном щитке помещения.
Первый вариант лучше, потому что дает возможность перемещать щепорез для арболита (с б/у или новым электродвигателем) в любое место, как полноценное оборудование.
Собираем узлы щепореза
Осуществляем сборку в следующей последовательности:
- Собираем рубильный блок: на вал насаживаем подшипники, диск с ножами и молотки;
- Подготавливаем корпус к монтажу: вырезаем отверстия для рабочего вала, приемного бункера и выгрузки щепы;
- Сверлим необходимые отверстия для сборочных болтов и привариваем под углом воронку приемного бункера;
- Производим сборку привода: закрепляем двигатель на раме, монтируем шкивы и надеваем ремень (можно автомобильный);
- Крепим рубильный блок на раму и закрываем защитным корпусом (во избежание несчастных случаев);
- Производим холостой пробный запуск.
Щепорез для арболита в сборе
В течении первой недели рекомендуется использовать щепорез для изготовления арболита в режиме минимальной нагрузки и недолгое время, чтобы избежать заклинивания подшипников, которое может произойти в результате их перегрева.
Если станок нужен исключительно для собственных целей, то есть смысл сделать шепорез для арболита своими руками, так как если приобретать его в заводском исполнении, то обойдется он не очень дешево. Сделанный щепорез можно поставить под навесом на приусадебном участке или в гараже.
По материалам: https://zamesbetona.ru/oborudovanie/shheporez-dlja-arbolita.html
https://kamedom.ru/arbolit/chertezhi-stanka-scheporeza.html
Метки: арболит , монолитный арболит , своими руками , станок , щепа , щепорез
Конструкционные особенности
При изготовлении самодельного щепореза чертежи и схемы будущей машины являются незаменимым помощником. В большинстве случаев народные умельцы создают приборы с питанием в 220-380 В, которое состоит из таких деталей:
- Корпус из металла со съемным кожухом.
- Биты с молотками, которые состоят из нескольких секций, разделенных отбойниками.
- Диск с режущими элементами — ножами.
- Сито с отверстиями соответствующего размера для просеивания щепы.
- Резервуар для загрузки древесных отходов.
Устройство щепореза может отличаться наличием тех или иных деталей, но общий принцип действия остается аналогичным. При подаче напряжения в 220 В электродвигатель начинает вращаться, запуская вращение барабана с лезвиями. Все, что требуется от человека — вовремя засыпать в резервуар отходы древесины.
После успешной сборки щепореза можно обустроить автономную систему производства щепы длиной до 25 миллиметров и шириной 5 мм. Такой материал станет хорошей основой для изготовления арболитовых блоков или монолитного арболита.
Где брать чертежи с размерами?
На некоторых форумах (в частности приведенных в этой статье) пользователи предлагают уже готовые чертежи роторно-барабанного щепореза для производства щепы для арболита или копчения за небольшую оплату, но их можно найти и бесплатно.
Кроме того, человек, разбирающийся в слесарных работах на уровне опытного ученика и владеющий черчением на школьном уровне, сможет составить чертеж самостоятельно, учтя при этом особенности доступного материала.
Поэтому любой, кто знает, как сделать веткоруб или щепорез для дальнейшего производства арболита или другого применения изготавливаемой им щепы своими руками, и уверен, что способен сам собрать такое устройство, без проблем сможет сделать и его чертеж.
Тем более, что изготовление деталей и общий монтаж самодельной щепорезки по чертежу гораздо проще, чем без него, даже если есть вспомогательное видео.
Читайте также: Сверло для высверливания точечной сварки. Особенности заточки
Преимущества самодельной дробилки
Самодельные изобретения по принципу работы напоминают обычную электрическую мясорубку, а для их изготовления достаточно подготовить:
- Металл для создания основных частей (можно использовать металлические уголки или отрезки трубы).
- Около 20 дисковых пил.
- Пару шкивов.
- Шпильку из прочного металла.
- Подшипники.
- Ремень или цепь.
- Гайки.
- Шайбы.
- Баллон с краской.
В качестве двигателя можно использовать и дизельные, и электрические модели. Главное, чтобы они выдавали требуемую мощность и не нуждались в дорогостоящем обслуживании. Конечно же, лучше отдать предпочтение электродвигателям, так как они более безопасные и легкие. К тому же, при работе электромотора отсутствует лишний шум. Что касается дизельных двигателей, то они характеризуются высокой мощностью и автономностью, но работают очень шумно и выделяют выхлопные газы во время работы.
Щепорез — это полезный инструмент для частного хозяйства, но покупать его за несколько миллионов рублей не совсем целесообразно. Поэтому лучше попытаться изготовить конструкцию своими руками, так как это не требует больших финансовых вложений или усилий.
Какой должна быть щепа?
Древесный наполнитель для арболита имеет свой ГОСТ. На уровне государственного стандарта для щепы установлены жесткие требования.
Выделены три основных параметра:
- длина не больше 30 мм;
- ширина не больше 10 мм;
- толщина не больше 5 мм.
Обозначены и оптимальные размеры по ширине и длине:
- длина – 20 мм;
- ширина – 5 мм.
Новые требования появились с принятием ГОСТ 54854-2011. До этого существовал другой ГОСТ с меньшими требованиями. Тогда допускалось использование более длинной щепы – вплоть до 40 мм. В 2018 году «вольности» в размерах наполнителя не допускаются.
Стандарт регламентирует и наличие примесей: коры, листьев, хвои. Материал следует очищать от земли, песка, глины, а в зимнее время – от снега. Наличие плесени и загниваний недопустимо.
Требования к дробильным машинам
Подготовив чертежи и схемы щепореза для арболита, можно приступать непосредственно к его изготовлению. Отдельные элементы машины вытачиваются с помощью токарного оборудования, а все остальное вполне возможно сделать из подручных средств в домашних условиях.
Для начала нужно найти подходящую силовую установку, которая обладает мощностью 4-5 кВт. Что касается параметров ременной передачи, то их определяют с учетом количества шкивов. В любом случае, максимально допустимое число оборотов должно составлять как минимум 1700-1800 об/мин. Для повышения безопасности эксплуатации прибора все режущие элементы нужно защитить сплошным кожухом из стали.
Наличие муфты в приводной системе не предусмотрено. Объясняется это тем, что при моментальном выключении машины внутри могут остаться частички щепы, которые останутся в зазорах и существенно поднимут пусковой момент двигателя. Подобное явление может привести к перегреву и полному повреждению силовой установки.
В качестве режущего диска используют модели из толстолистовой стали, диаметр которой составляет 10-12 мм. Помимо основного предназначения, этот элемент выполняет функции маховика, поглощая неравномерное вращение вала при застревании щепы. Внутреннюю часть диска тщательно шлифуют.
При создании режущих элементов в домашних условиях задействуют инструментальную сталь под марками У7А или У8А. Показатели твердости ножей после заточки должны составлять 58-60 HRC. Заточка должна бить односторонней, а высота рабочей кромки не должна превышать высоту установочных пазов диска. Для простоты наладки и регулировки инструмента крепежные отверстия в ножах делают овальными.
Сито создается из высокоуглеродистой стали под марками от 40. В готовом стальном листе проделываются отверстия, через которые будет пропускаться исходное сырье. При изготовлении рубильных молотков рекомендуется использовать рессорно-пружинную сталь. Но чрезмерная упругость может привести к инерционному подбрасыванию режущих элементов во время работы. Из-за высокой скорости вращения рабочего вала такое явление может ухудшить конечное качество продукта, поэтому лучшим решением для рубильных молотков станет инструментальная сталь.
Покупка прибора
При желании приобрести щепорубительную машину в магазине необходимо понимать, что она может стоить очень дорого. Средняя стоимость заводской модели составляет около 3 миллионов рублей. Естественно, такое оборудование демонстрирует высокую производительность, но для бытовых целей покупать его нецелесообразно. Вместо этого лучше найти отдельные агрегаты для сушки, дробления и окрашивания щепы, что обойдется в разы дешевле.
В зависимости от способа измельчения исходного сырья дробилки бывают дисковыми и роторными. Представители первой группы оборудованы острыми дисковыми ножами, в то время как роторные модели работают на основе вращающейся рабочей камеры или барабанов, где находятся ножи.
Выбирая подходящий вариант дробильного оборудования, важно обращать внимание на толщину корпуса. Желательно, чтобы она составляла не меньше двух сантиметров в месте режущего узла. В противном случае при работе на высоких оборотах механизмы могут деформироваться или вовсе выйти из строя.
Что касается ножей, то они должны быть из высокопрочной стали с высокой степенью износостойкости. Для бытовых целей вполне хватит щепорезки с двумя и больше ножами.
Четыре вида щепореза
- Винтовой (шнековый). Попадающие в агрегат ветки перемалываются крутящимся винтом. По такому принципу работает обычная мясорубка.
- Дисковый. Закреплённые на валу диски перерубают древесину в щепку. Аналогичным образом работают кухонные комбайны и блендеры.
- Роторно-молотковый. Куски древесины, разрезанные на части ножами маховика, дробятся затем в щепу установленными на роторе молоточками.
- Барабанный. Измельчение происходит ножами, закрепленными на внутренней поверхности барабана, в который попадает дерево.
Формирование блоков перемычек
В подходящие формы раствор заливается с помощью ведер или лопат. Трамбовочное приспособление создается из бруса и применяется только после полного заполнения емкости раствором с образованием небольшой горки сверху.
Не нужно проводить трамбовку после выливания каждого слоя. Хаотичность смеси обеспечивает высокое качество. При укладке можно немного прижимать отдельные участки, чтобы материал плотно укладывался. Трамбовка неполной формы является ошибкой и приводит к разграничению слоев и низкому качеству их схватывания.
Смесь должна побыть в форме 2-3 дня, после чего ее нужно демонтировать и поместить содержимое на открытый воздух для просушивания. При отсутствии финансовых ограничений рекомендуется приобрести вибростол, обеспечивающий уплотнение материала в формах.